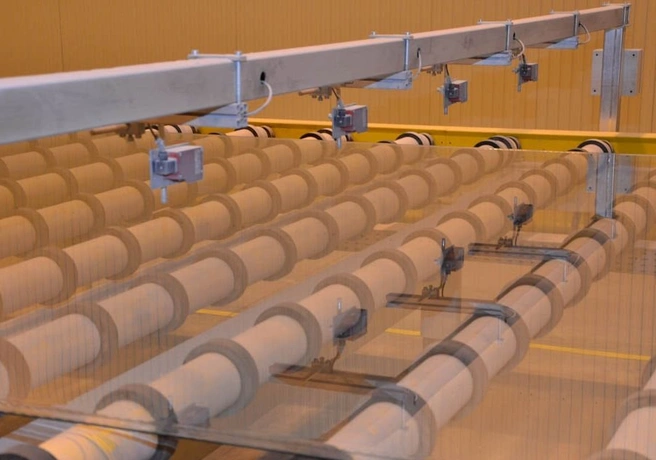
Королевство зеркал бывает не только в сказках. И пусть попасть туда не так-то просто, иногда удается найти возможность проникнуть в зазеркалье. В Рязани с 2008 года работает уникальный в своем роде стекольный завод фирмы «Гардиан». Побывать по ту сторону процесса производства стекла и зеркал удалось корреспонденту YA62.ru. О том, как не заблудиться в зазеркальном королевстве рассказала Юлия Смирнова, специалист по маркетингу компании «Гардиан».
Начинается процесс производства стекла с того, что сырье (кварцевый песок, стеклобой, соду, доломит и другие ингредиенты) смешиваются в определенных пропорциях в составном цеху. Из приемного бункера шихта подается в печь. Нагреваясь до 1 610°C, шихта плавится, образуя стекломассу.
В зоне максимальных температур температура огнеупора составляет порядка 1 600°C — 1 620°C, что всего в четыре раза холоднее поверхности Солнца. По краям градус другой, чуть меньше. Это сделано для того, чтобы масса, залитая в печь, самостоятельно перемешивалась от горячей к холодной и становилась однородной. Кроме того, с правой и левой стороны печи попеременно подается газ с определенным интервалом, который поддерживает ее температуру.
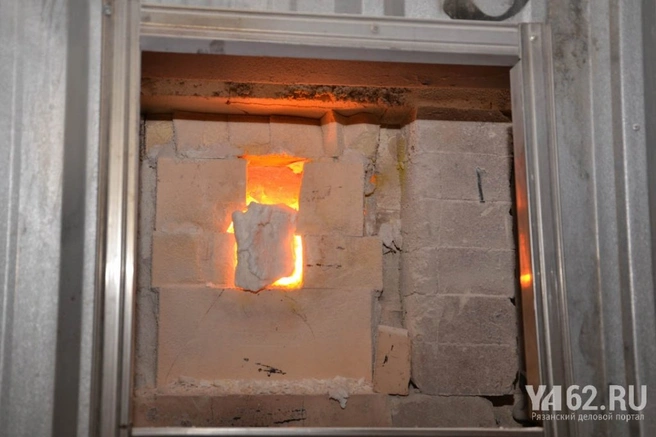
После этого жидкая стекломасса проходит процесс гомогенизации (становится однородной), охлаждается и выливается в оловянную ванну. Здесь температура порядка 950 °C. Плотность олова выше плотности содержимого печи, благодаря чему стекломасса распределяется по поверхности олова равномерным слоем. Эффект схож с тем, как капля масла растекается по воде. Это нужно для того, чтобы придать идеально ровную поверхность будущему стеклу. Оно будет без бугорков и ряби, без каких-либо вкраплений и примесей.
— Здесь же формируются толщина и ширина стекла. Без внешнего воздействия толщина стекломассы составляет 5,8-6 мм. Если нужно сделать тоньше — формировочные машины, меняя свой угол, распределяют ее от центра к краям, если толще — от краев к центру. Чем дальше плывет стекломасса, тем тверже становится, — замечает Юлия.
Следующий этап — лер отжига. Туда будущее стекло попадает ровным и горячим, только что из ванны. Теперь его нужно постепенно охладить, чтобы оно превратилось в конечный продукт температуры не больше 50 °C. Все это делается очень медленно и плавно, чтобы стекло не лопнуло от резкого перепада температурного режима. Что представляет собой лер отжига? Это длинный конвейер, по которому медленно движется стекло.
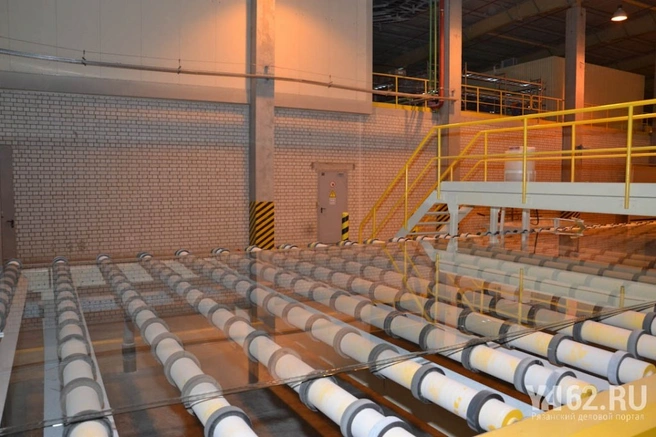
После того, как стекло охладилось и достигло своей оптимальной кондиции, самое время отправить его в цех резки. Естественно, процесс осуществляется с помощью специальных ножей, которые изначально направлены не вертикально, а под углом, чтобы стекло можно было резать прямо в момент его движения. Тогда срез получается идеально ровный, прямой.
Интересно, что весь процесс приготовления стекла непрерывен. Завод работает семь дней в неделю, 365 дней в год. Производство не останавливается ни на минуту, и стекло идет постоянно, бесконечным потоком.
Момент резки стекла сопровождается также компьютерным контролем, который на данном этапе немаловажен. Происходит досмотр на наличие инородных вкраплений, микротрещин, сколов. Если стекло не проходит установленные заводом стандарты, оно отправляется обратно, в топку, где ему предстоит сделать очередной круг жизни.
— Стандарты качества «Гардиан» выше, чем ГОСТ, поэтому на квадратный метр стекла у нас приходится гораздо меньше брака. И даже если по ГОСТу продукт бы считался качественным, то по правилам нашего завода такое стекло отправится снова в печь, — не без гордости рассказывает мой экскурсовод.
По сути, флоат-стекло готово. Но! Визитной карточкой фирмы «Гардиан» считается стекло с напылением. Существует два направления: ClimaGuard и SunGuard. Первое — это энергосберегающее стекло для частного сектора, жилых помещений. Второе — архитектурное стекло с магнетронным напылением.
— Существует распространенное мнение, что чем больше в квартире окно, тем холоднее будет зимой, потому что через стекло уходит и часть тепла. Наша компания ломает стереотипы, предлагая жителям России стекло с напылением, позволяющее снизить потери тепла, сводя тем самым энергозатраты к минимуму. С нами сотрудничают уже многие фирмы, которые занимаются установкой стеклопакетов. Такое стекло по цене не сильно отличается от обычного, но в результате использования, можно сэкономить приличную сумму на отоплении и кондиционировании, — отмечает маркетолог «Гардиан».
Стекла производят с низкоэмиссионным покрытием, в основе которого высокопробное серебро, что позволяет обеспечить превосходные теплосберегающие свойства.
SunGuard чаще всего используется в архитектурном строительстве. К примеру, в России из такого стекла были построены объекты Олимпиады в Сочи, возводится башня «Эволюция» в Москва-Сити. В Рязани фасад «Барс Премиум» выполнен стеклом SunGuard.
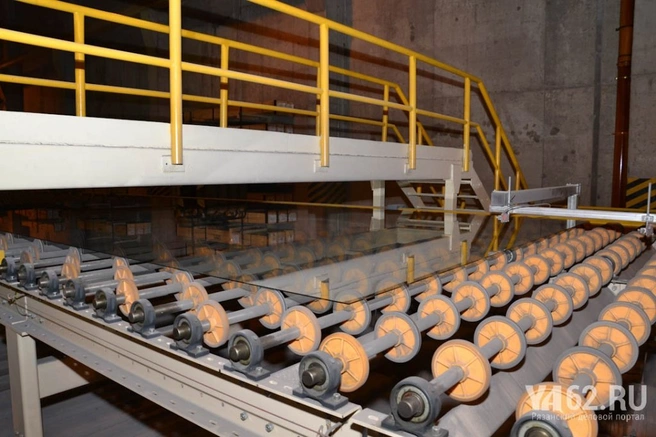
После того, как на стекло нанесено необходимое покрытие, оно проходит процессы мойки, сушки и окончательного осмотра. Специально обученный робот укладывает готовый продукт в стопки, которые упаковываются пленкой и деревянными каркасами. Эти брикеты транспортируются на склад, откуда и вывозятся на продажу по городам и весям.
— Мы выпускаем стекло разного размера, — поясняет Юлия Смирнова. — Самое большое — джамбо-стекло: три на шесть метров, от английского «Jumbo», то есть «гигантское, крупногабаритное». Для его вывоза используются специальные фуры, способные вместить именно такой размер.
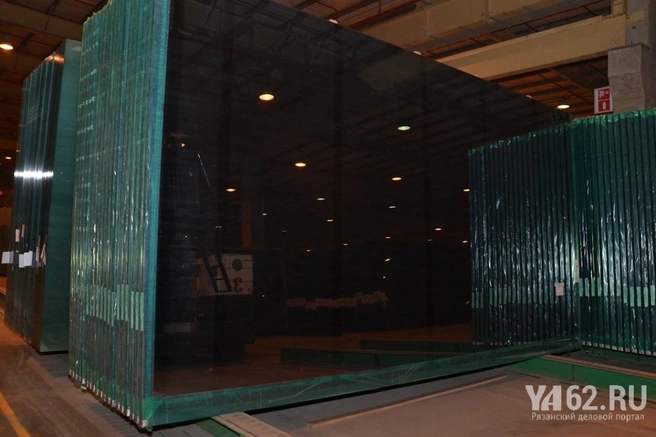
Однако готовое чистое стекло идет не только на конвейер для напыления, но и отправляется на линию по производству зеркала.
— Наша линия — волшебная, потому что при загрузке имеем прозрачное стекло, а на выходе — самый магический предмет, используемый в быту — зеркало. Сейчас зеркала — это не только предметы обихода, интерьера и декора, зеркала широко используются в военной, космической и других отраслях. Здесь серьезно налажен процесс производства и контроля качества продукции.
Итак, робот-загрузчик выкладывает листы на конвейер, затем автоматически двигаются по линии в секцию, где происходит первая стадия подготовки поверхности стекла — смыв сепарирующего порошка (вещества, которое наносится на стекло, чтобы листы не слипались друг с другом).
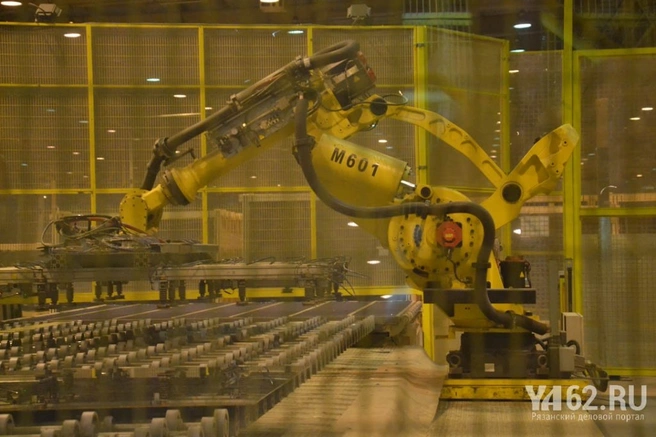
После этого листы стекла направляются в секцию полирования при помощи полировочных мостов для тщательной подготовки поверхности для нанесения активатора.
Затем листы двигаются в камеры нанесения серебра и меди, где происходит нанесение металлов методом распыления растворов. Это важные процессы стадии в изготовлении зеркала. Именно в них закладывается самый важных критерий годности зеркала – коэффициент отражения.
В камере серебра молекулы активного серебра соединяются с молекулами олова и оседают на поверхности, как бы наслаиваясь друг на друга.
Но металлическое серебро быстро окисляется и со временем становится темным. Слой серебра защищается слоем металлической меди. Затем идет процесс интенсивной промывки после всех химических процессов.
После мойки, будущее зеркало попадает в печь, в которой оно нагревается до температуры около 100 °C для полного обезвоживания металлизированной поверхности.
Дело остается за малым — нанести слои краски на заднюю сторону зеркала.
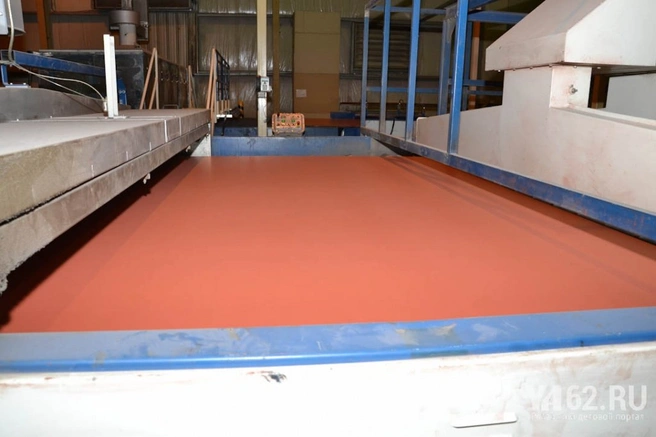
— Мы используем два слоя. Первый слой — красный, для защиты зеркала от коррозии при эксплуатации, второй — синий, для защиты от механических повреждений. Каждый слой запекается в печи, чтобы краска высохла и полимеризовалась. Температура в печи более 200°C. Поэтому затем зеркала охлаждаются мощными воздушными вентиляторами и системой водяного охлаждения, — рассказывает Юлия.
Далее зеркала проходят через секцию финальной мойки. Каждый лист зеркала маркируется для идентификации продукции с нанесением штрих-кода даты и времени изготовления.
Осталось пройти только пристальную проверку «зоркого глаза» оператора контроля качества на специально оборудованном участке, от которого не ускользнет незамеченным ни один дефект. Далее при помощи робота выгрузки формируются пачки готового зеркала, затем они упаковываются в деревянную тару. На каждую пачку зеркала прикреплен сопроводительный документа с указанием полной информации о продукте.
Все — зеркало готово, можно отгружать.
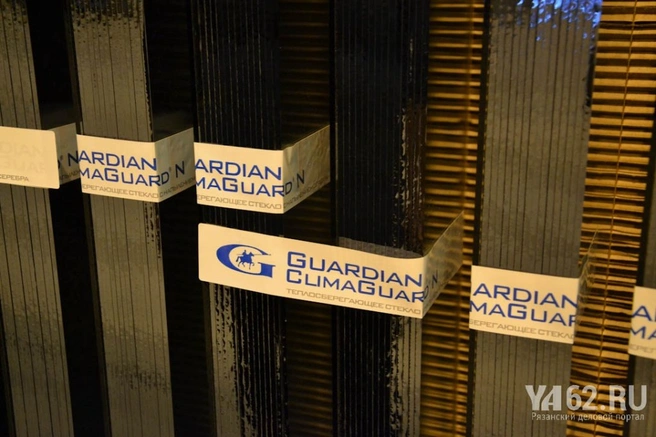
На складе, как оказалось, легко заблудиться. Здесь повсюду настоящее зазеркалье: куда ни посмотри — везде стопки стекла, превращающие отражение друг друга в коридоры. Отлично место для того, чтобы сделать самое крутое селфи в стране.
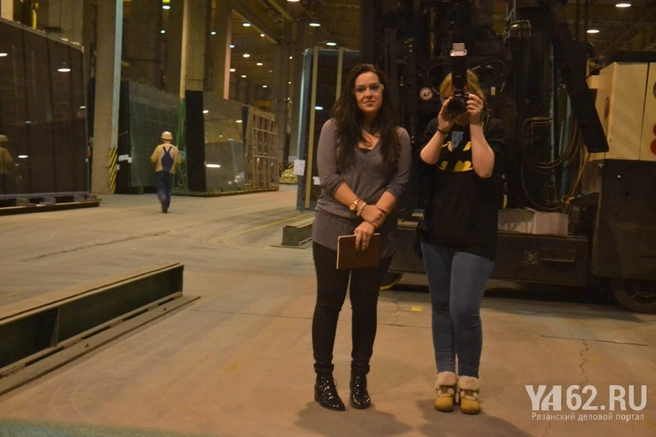
Говорят, на стекольном заводе работают хрупкие и ранимые люди. Но ко всему прочему, наверное, еще и очень спокойные. Общий гул работающих машин сопровождается периодически повторяющимся звуком бьющегося стекла. Ничего особенного, просто бракованные модели отправляются на второй круг, но как же это успокаивает!
Побывала в зазеркалье Дарья Копосова
Больше фото ЗДЕСЬ