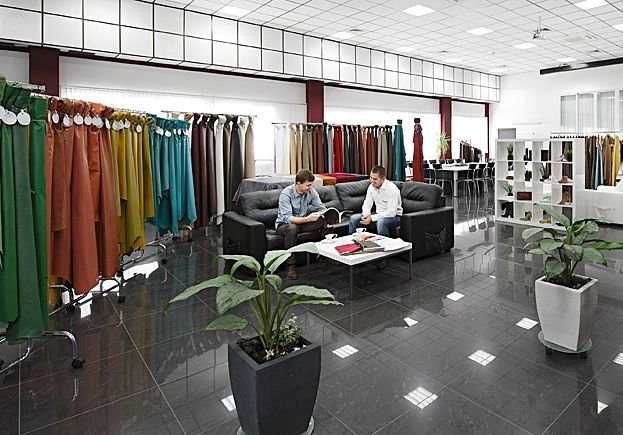
Подходя к огромному зданию кожзавода, сразу понимаешь, что с чувством юмора у руководства все в порядке. Первой, кто встретил меня у входа на предприятие — была... корова! Слава богу, не настоящая, хотя и выглядит вполне реалистично. Скульптура в виде этого животного является главным украшением газона и символом производства. Установленная рядом табличка гласит: «КОРМИЛИЦА». Дело в том, что из шкуры этого известного всем молочного животного здесь и делают кожу всевозможных фактур и оттенков.
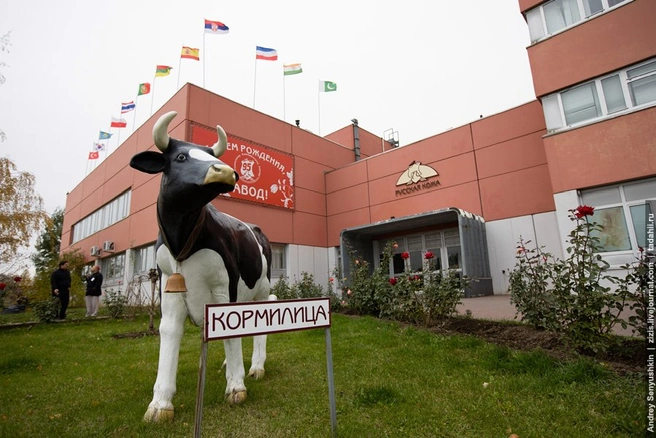
Кожаные консервы
Экскурсия по самому производству началась для меня в цехе начальной обработки сырья. Один этап пришлось пропустить, но мне подробно рассказали, что на нем происходит. Итак, в первую очередь сырье, поступившее на завод, проходит через ПОКС (цех первичной обработки кожевенного сырья). Вести туда меня отказались, так как находится он в отдельном здании, да и процесс, как выразился технолог, «не самый эстетичный».
На ПОКСе шкуры помещают в устройства в виде больших полых барабанов, которые, вращаясь, стряхивают с сырья грязь и лишнюю соль. Потом работники цеха обрезают с них лбы, щеки и хвосты. После этого шкуры сортируют по наличию дефектов, которые могли быть получены животным при жизни или после смерти — это в основном царапины или сдиры. Из ПОКСа партии сырья в законсервированном виде поступают в цех начальной обработки, куда мы и отправились.
Крутится барабан
Устройства, которые носят название барабанов и имеют соответствующую форму, есть в нескольких цехах завода. Отличаются они по размеру и назначению. В цехе начальной обработки установлены самые большие — в них с помощью автопогрузчика помещают сырье. Процесс этот называется страшным словом «отмокозоление» и длится от 30 до 40 часов.
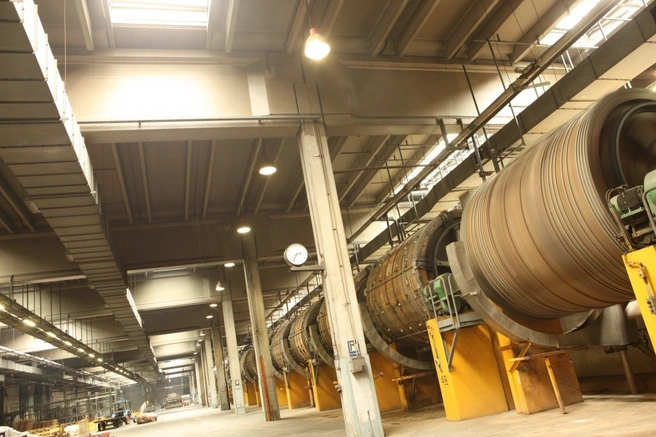
Но самом деле ничего страшного в нем нет. Состоит он из двух этапов — отмочки и золения. Сначала в барабанах, которыми можно управлять с помощью пультов из операторской, шкуры отмывают специальными химикатами. С сырья смывается оставшаяся грязь и консервирующие реагенты, это максимально щадящая обработка сырья, барабаны находятся в покое или медленно вращаются. Так сырье приводят к парному состоянию — таким оно было, когда его сняли с животного.
В процессе золения со шкуры удаляются волосы. После этого из барабанов сырье достают голым. В таком виде шкура называется гольём.
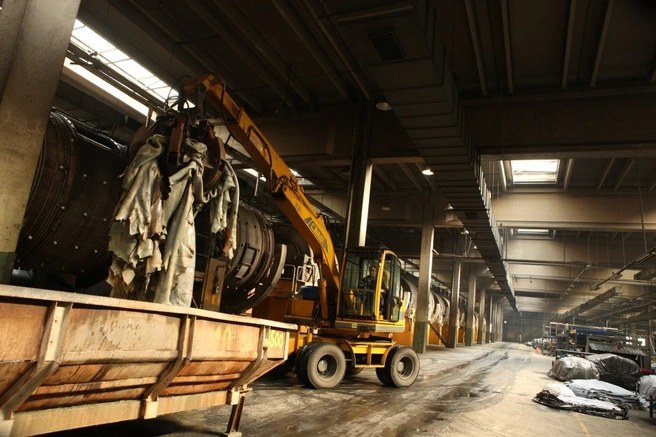
После этого сырье погружают в кассеты, подвешивают на цепи и отправляют на следующий этап. С помощью специального механизма они «едут» над цехом. Перед мездрильной машиной кассеты спускаются, и рабочие заправляют в нее сырье. Это следующий этап начальной обработки кожи.
Мездрильная машина состоит из двух ярусов, а внутри у нее два ножевых вала. Сначала кожа прижимается к одному из них, он вращается и срезает привязи мяса и сала. Когда с первой половины шкуры все лишнее удалено, она попадает на второй нож, где обрезается все остальное. После этого этапа остается только та часть, из которой потом производится кожа.
Мы переходим в следующий цех. Их здесь немало, и все они размещены в том же порядке, в котором следуют этапы производства. Здесь идет процесс дубления. Он так же проходит в барабанах, только крутятся они гораздо быстрее. Основная цель дубления, в результате которого получают полуфабрикат Wet-Blue, зафиксировать белок кожи солями хрома. Этот химикат придает коже голубой цвет. За него полуфабрикат и получил свое название. После такой обработки кожа становится высокопрочной и выдерживает температуру свыше 100 градусов. По словам технолога кожзавода, 90% кожи производится именно из этого полуфабриката, хотя здесь готовят не только его. Например, Wet-White. Его дублят с помощью других химматериалов, и он имеет белый цвет. Получается экологически безопасный материал, который используют для автосалонов и детской обуви.
Предок велюра
Из барабанов полуфабрикат отправляется на выстилку. Рабочие завода раскладывают кожу по поддонам размером с большой обеденный стол. Это необходимо, чтобы стекла излишняя влага и хром равномерно распределился по слоям. Потом кожу отжимают. Ее заправляют в специальную машину. Большие валы крутятся и отжимают с кожи влагу. Теперь полуфабрикат поочередно выкладывают на измерительную ленту, где специальный прибор считывает размер полезной площади. Отсюда сырье поступает на сортировочный стол. Быстрого взгляда и показателей на мониторе специалистам завода хватает, чтобы определить сорт кожи.
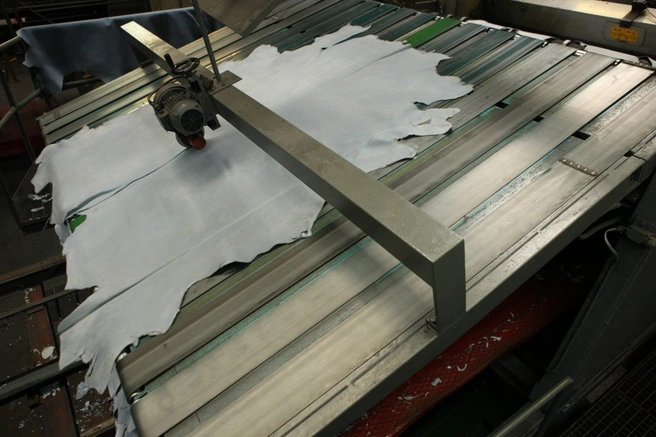
Следующий этап — двоение. Здесь полуфабрикат на специальной машине разделяют на две части. Из верхней потом сделают лицевую кожу, а из нижней, которая называется спилок, получится велюр. Чтобы выравнять толщину материала, его отправляют на строгальные машины. Затем снова проводят сортировку и измерение. Эти операции необходимы после каждого этапа обработки, чтобы оценить потери и заново присвоить сорт.
Сушка для краста
Следующий этап обработки кожи — процесс крашения-жирования. Жируют кожу и окрашивают в необходимый цвет в барабанах, которые здесь крутятся гораздо быстрее, чем в остальных цехах. Достают оттуда уже краст — это практически готовая кожа. Технологии получения этого продукта зависят от назначения: мебельная кожа должна быть эластичной, галантерейная — более жесткой. Краст доставляют в первоотделочный цех. Там его сушат и шлифуют.
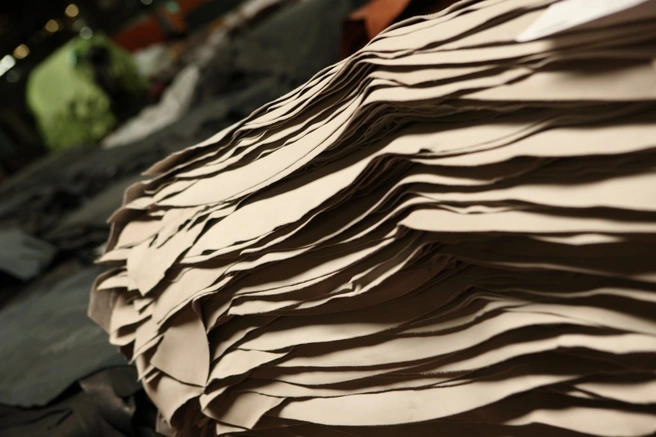
Существует несколько типов сушки. В классическом варианте — кожа снова попадает на разводную отжимную машину, а затем раскладывается на вакуумных столах, где выпрямляется под действием температуры. Машина для вакуумной сушки — многостольная: один поднимается, на другой выкладывают влажный краст, а с третьего забирают уже сухой. После этого кожа все еще недостаточно сухая, и рабочие завешивают ее в так называемую атмосферную сушку.
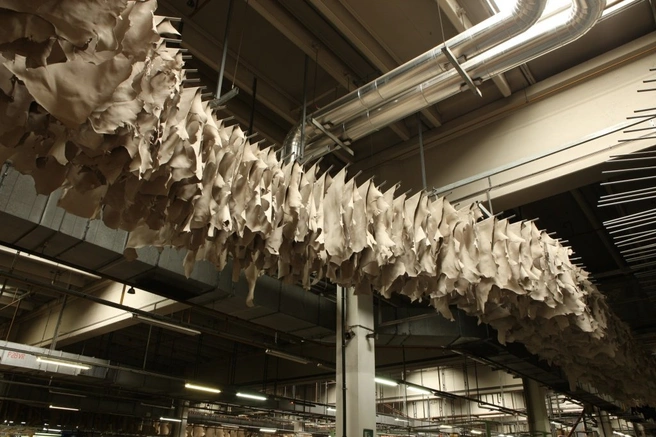
Большие цветные куски кожи рабочие крепят на вешалки. Весь первоотделочный цех буквально завешан ими. Они и на специальных карнизах, и под потолком. Для лучшего эффекта кожа на вешалках может проезжать по специальным тоннелям.
После этого она высыхает, но приобретает определенную деформацию. Чтобы это исправить, кожу отправляют на тяжку. С помощью небольшого прибора, напоминающего электробритву, мастера выравнивают края, удаляют неровности и обрезают поврежденные участки.
Здесь же, специальная машина с помощью мелких уголков как бы «расчесывает» кожу, расправляя склеившиеся волокна.
Второй вариант сушки проводят, закрепив кожу на раме в человеческий рост с помощью прищепок. Это делается быстро, а потому задействованы сразу несколько человек. Раму с кожей отправляют в тоннель для сушки.
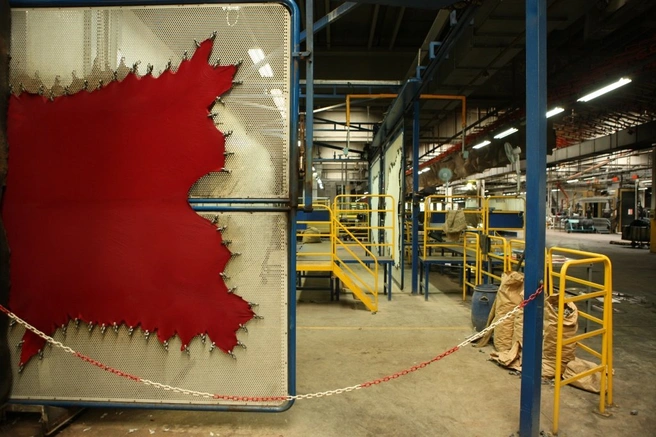
Отшлифовать до блеска!
Мы отправляемся в цех финишной обработки, куда поступает высушенная кожа. Здесь на нее наносят различные покрытия и эффекты. Отсюда выходит уже готовый материал. Вы ведь помните, что кожа бывает разной и на вид, и на ощупь? Можно купить гладкие лакированные ботинки, сумку с рисунком и «зернистый» кошелек.
Это зависит от вида тиснения. Покрытие на кожу здесь наносят двумя способами. В первом случае ее загружают в валичную машину, на вид она практически не отличается от тех, которые используются для отжима. Прибор прижимает кожу, прокатываясь по ней, и придает материалу нужный эффект. Второй способ выглядит куда более интересно. Да и процесс масштабнее. В ряд установлены прозрачные квадратные камеры, через которые по очереди проезжает кожа. Внутри каждой из них — механизм с несколькими пистолетами. Они вращаются и распыляют по коже химические вещества, которые создают нужный эффект.
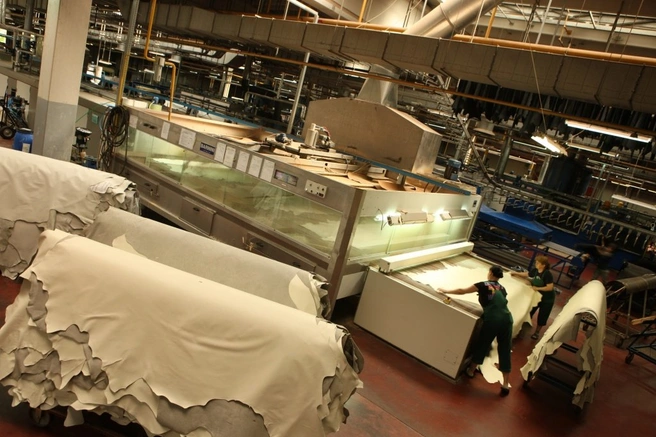
Это могут быть различные рисунки-тиснения. Готовые кожи достают из машин и снова отправляют на сушку. Финишная обработка, как и все остальные этапы, завершается измерением и сортировкой.
Здесь же висят готовые кожи — разного цвета и разной текстуры. Сортировщики раскладывают ее по сортам, ориентируясь на уже готовый образец. Теперь кожа отправляется на склад готовой продукции, откуда ее потом доставят заказчикам.
Испытания для будущего ботинка
Посмотрев на то, как из шкуры получается красивая цветная кожа, отправляемся в испытательный цех, где все процессы можно наблюдать в миниатюре. Здесь установлены мини-версии барабанов – от метровых до совсем крошечных. Работники этого цеха отрабатывают новые технологии и пробуют наносить разные цвета. Для этого используют обрезки, которые остаются после основных этапов производства. На маленьких кусочках пробуют новые химматериалы, наносят цвета и тиснения.
Из испытательного цеха идем в лабораторию. В первом кабинете тестируют сточные воды и условия на рабочих местах, в том числе воздух промзоны.
Во втором кабинете идет гораздо более увлекательная работа. С помощью специальных приборов тестируют кожу, сделанную на предприятии.
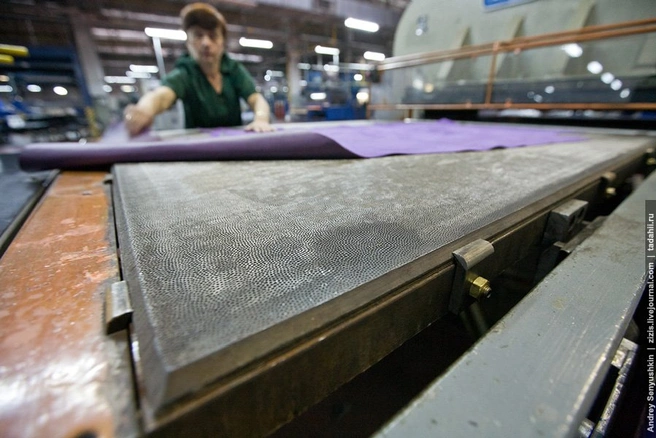
Вот, например, флексометр. Этот прибор проверяет кожу на устойчивость к многократному изгибу. Небольшой кусочек помещают внутрь и имитируют изгибы обуви при естественной ходьбе. Это позволяет определить, насколько прочен материал и как быстро износится.
На заводе также производят гидрофобную кожу, которая отталкивает воду и не промокает. Кусочек материала помещают в другой прибор, он наполняется водой и останавливается после того, как кожа промокнет.
В лаборатории есть приборы, которые проверяют, как фетр, полученный из спилока, выдерживает трение, насколько быстро он истирается и пачкается. Чтобы условия окружающей среды не повлияли на оценку, здесь установлена специальная камера.
Еще один аппарат позволяет понять, что будет с обувной кожей в мороз, и какие температуры она сможет выдержать.
Вуаля!
Территория оказалась огромной, и, чтобы обойти все цеха, потребовалось полтора часа. Неудивительно, что рабочие передвигаются по заводу на велосипедах, которые мне не раз довелось встретить, изучая этапы создания кожи. Мое путешествие закончилось в шоу-руме, где представлены образцы готовых кож и сделанных из них вещей. На застекленных витринах – сувенирная продукция. На полочках красуются ежедневники и книги в кожаном переплете. Детские цветные ботиночки, элегантные туфли, сапожки и сумки всевозможных фасонов.
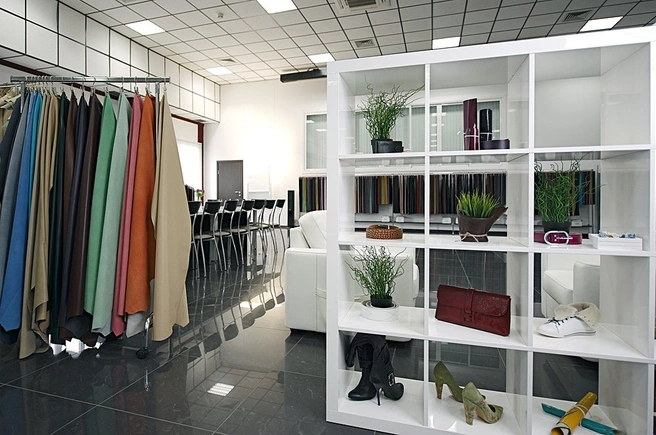
Есть здесь и отдельный стенд с ремнями. По комнате расставлены кожаные диваны, а у окна можно найти автомобильные кресла, обтянутые той самой кожей, к которой предъявляют наиболее жесткие требования. Бесконечные вешалки пестрят многообразием цвета и фактуры. И глядя на все это великолепие, на этот зал славы кожзавода, сложно представить, что такая красота получилась из того, что когда-то было неприметной коровьей шкурой.
Гуляла по цехам кожзавода Екатерина Локтюшова